ساخت افزایشی فلز امکان تولید قطعات پیچیده را فراهم میسازد. در روشهای تولید قدیمی محدودیتهای خاصی در طراحی قطعه داشتیم ولی در روش پرینت سه بعدی هر قطعه ای با هر هندسه ای را می توان تولید نمود.
ساخت افزایشی به نام پرینت سه بعدی نیز شناخته میشود؛ اما خوب است بدانیم که ساخت افزایشی کلمهای کلی تر است و روشهای زیادی را در بر میگیرد. این روش برای تولید قطعات پیچیده بسیار پرکاربرد است.
بهینه سازی طراحی با ساخت افزایشی
روش ساخت افزایشی باعث شده تا طراحی قطعات صنعتی متحول شود. در روشهای تولید قدیمی با توجه به اینکه امکان تولید قطعات مورد نظر با طراحی هندسی لازم وجود ندارد طراحی قطعه را تغییر میدادند.
اما امروزه دیگر شکل هندسی قطعه باعث ایجاد محدودیت در تولید آن نمیشود. چون به لطف وجود ساخت افزایشی تولید هر شکلی امکانپذیر است. مثلا در شکل زیر دو طراحی مختلف از یک قطعه مورد استفاده در هواپیمای ایرباس را مشاهده میکنید. قطعه جلویی یک طراحی بهینه شده از قطعه است که با ساخت افزایشی تولید میشود. اما قطعهای که در عقب تصویر میبینید چون بدون روش ساخت افزایشی تولید شده، طراحی متفاوت و با وزن بالاتری دارد.
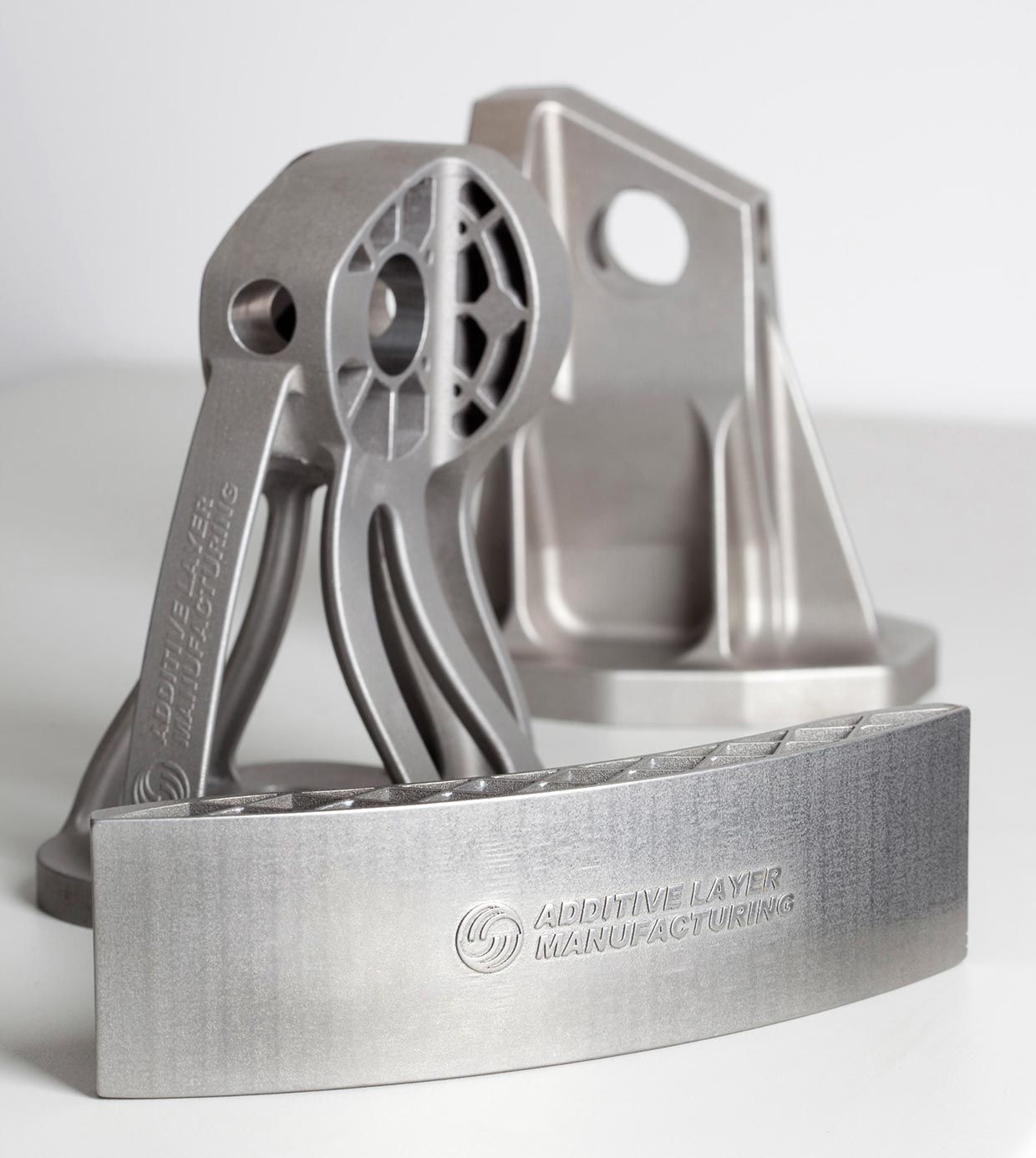
تولید انبوه با ساخت افزایشی
قطعاتی که تا همین چند سال پیش امکان تولید آنها وجود نداشت اکنون با روش ساخت افزایشی تولید میشود. ساخت افزایشی به عنوان روشی بسیار مناسب برای تولید قطعات پروتوتایپ (نمونه اولیه) شناخته میشود. اما اکنون میدانیم که این روش برای تولید انبوه نیز به کار میرود. در ساخت افزایشی فلزات از پودرهای فلزی برای تولید قطعه استفاده میکنند. در این روش میتوان از پودرهای مختلف فلزی همچون فولاد، آلومینیوم، نیکل و … استفاده نمود.
«ساخت افزایشی فلزات» عمدتا با نام «پرینت سه بعدی فلزات» شناخته میشود؛ کاربرد این دو عبارت به جای هم تا حدی درست است و به همین دلیل ما نیز در بسیاری موارد این دو عبارت را به جای هم به کار میبریم. در ساخت افزایشی قطعات 3بعدی به صورت لایه لایه تولید میشوند. برای تولید قطعات فلزی به روش ساخت افزایشی از پودرهای فلزی استفاده میشود، اما گاها در بعضی از روشها کمی ماده پلیمری نیز برای کمک به فرآیند ساخت قطعه استفاده می شود.
در این وبسایت سعی شده اطلاعات جامعی در زمینه ساخت افزایشی فلزات فراهم شود. ساخت افزایشی فرآیندی است که در آن مواد به یکدیگر متصل میشوند و منجر به تولید قطعه 3 بعدی میشوند. این روش مقابل روشهای قدیمی تولید همچون ماشینکاری و شکلدهی است. در روشهای قدیمی همچون ماشینکاری از یک قطعه بزرگ کاسته میشد تا شکل نهایی مورد نظر حاصل شود {(به کد ISO/ASTM 52900:2021) رجوع شود. }
در سات افزایشی یک قطعه 3 بعدی در تعداد مراحل کمی تولید میشود. برای تولید قطعه در این روش کافی است که فایل طراحی کامپیوتری قطعه (CAD) را داشته باشید. این فایل از طریق نرم افزارهای رایج طراحی همچون سالیدورکز، کتیا و … به آسانی به دست میآید. سپس این فایل به ماشین ساخت افزایشی داده و قطعه تولید میشود.
مزایای ساخت افزایشی
ساخت افزایشی مزایای زیادی نسبت به روشهای تولید سنتی همچون ریختهگری، شکلدهی، ماشینکاری و … دارد. امکان تولید قطعات با اشکال هندسی پیچیدهتر، وزن سبکتر و در عین حال عملکرد بهتر از مزایای ساخت افزایشی است. فرآایند ساخت افزایشی نیاز به ساخت ابزار و قالب برای تولید قطعه ندارد، در حالیکه همانطور که میدانیم در روشهایی همچون ریختهگری قالب و ابزارهای زیادی برای تولید قطعه نیاز است.
از ابداع روش ساخت افزایشی تنها حدود 30 سال میگذرد؛ بنابراین یک روش جدید و نوپا در مقایسه با سایر روشها همچون ریختهگری و آهنگری (فورج) که هزاران سال سابقه دارند محسوب میشود. گفتیم که این روش، جدید و نوپا است؛ اما در عین حال قطعات تولید شده با ساخت افزایشی با کیفیت هستند و در بسیاری موارد نسبت به سایر روشها همچون ریختهگری و شکلدهی کیفیت و استحکام بالاتری دارند.
در این روش میتوان به سرعت یک قطعه را تولید نمود. در روشهای قدیمی همچون ریختهگری به دلیل نیاز به قالب، ابزار و … فرآیند ولید بسیار زمانبر است؛ در حالیکه در این روش تنها به یک پرینتر 3بعدی نیاز دارید.
اولین پرینتر سه بعدی تنها قادر به ساخت مواد پلیمری بود. این دستگاه در سال 1987 ساخته شد و از رزین و اشعه لیزر برای تولید قطعات پلیمری استفاده مینمود.
استفاده از پودرهای فلزی در سال 1990 آغاز شد. برای ذوب پودرها از “لیزر CO2” استفاده میشد. میزان انرژی تامین شده توسط این لیزرهای قدیمی پایین بود و تنها در حدی بود که میتوانست پودرها را تا حدی خمیری شکل و زینتر نماید. به همین دلیل در آن بازه زمانی روشهای زینترینگ رایج شدند. اما قطعات تولید شده به روش زینترینگ دارای تخلخل در ساختار و چگالی پایینی هستند. کیفیت پایین قعات تولید شده با روش زینترینگ باعث میشود که برای کاربردهای صنعتی چندان مناسب نباشند.
قطعات تولید شده به روش زینترینگ به دلیل کیفیت پایین و وجود تخلخل در ساختار برای کاربردهای صنعتی چندان مناسب نیستند به همین دلیل قطعات روش زینترینگ چندان قابل اعتماد نبودند.
برای افزایش کیفیت قطعات لازم بود تا فرآیند ذوب کامل پودر صورت گیرد به همین دلیل لازم بود تا انرژی لیزر افزایش یابد. این مشکل با استفاده از لیزرهای فیبری “fiber” حل شد. لیزرهای فیبری توان و انرژی بالاتری دارند و به راحتی میتوانند پودرهای فلزی را کاملا ذوب و حتی بخار کنند.
با توسعه دانش لیزر و توان ذوب پودر نام فرآیند از زینترینگ انتخابی لیزر (SLS) به ذوب انتخابی لیزر (SLM) تغییر کرد. با توسعه دانش تولید به روش SLM، دیگر تولید قطعات فلزی دارای اشکال هندسی پیچیده کار دشواری نیست. در عین اینکه کیفیت قطعات نیز نسبت به روشهای سنتی بالاتر است.
انواع روشهای ساخت افزایشی فلزات
ساخت افزایشی فلزات به روشهای بسیار گستردهای تقسیم میشود. ساخت افزایشی بر دو اساس قابل دستهبندی است. در یک نوع دستهبندی بر اساس شکل مواد مصرفی تقسیمبندی میشود. شکل فیزیکی مواد مورد استفاده در ساخت افزایشی فلزات به ترتیب اولویت شامل موارد زیر میشود.
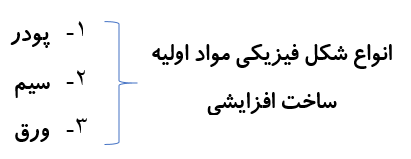
در ساخت افزایشی فلزات پودر و سیم تقریبا تما کاربرد را شامل میشود و میتوان گفت استفاده از ورق در ساخت افزایشی روشی حذف شده است و در عمل در صنعت کاربردی ندارد.
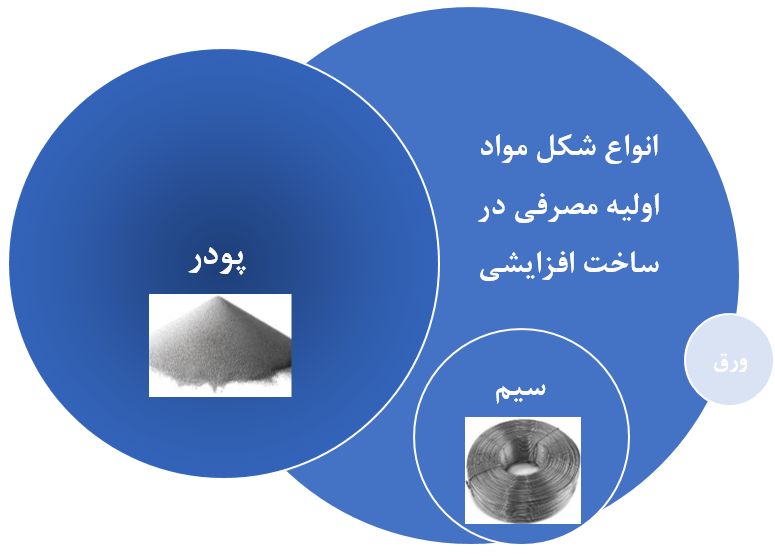
پس تا اینجا میدانیم که مواد اولیه مصرفی در ساخت افزایشی به دو شکل پودر و سیم رایج است. اما روشهای ساخت افزایشی بسیار متنوع هستند و بر اساس منبع انرژی که باعث ساخت و قرار دادن مواد اولیه در کنار هم میشود نیز تقسیم بندی میشوند. روش ساخت افزایشی فلزات بر اساس ذوب شدن نقطهای مواد اولیه فلزی و چسبیدن آنها به یکدیگر میباشد. این ذوب شدن نقطهای نیازمند انرژی بسیار زیادی است که باید در زمان بسیار کوتاه به پودر یا سیم در حال ذوب وارد شود. عمدتا انرژی بالا از طریق: اشعه لیزر، پرتو باریکه الکترونی و یا روشهایی همچون انرژی قوس تامین میشود؛ اما عموما در روشهای صنعتی ساخت افزایشی از منبع انرژی لیزر استفاده میشود.
روشهای ساخت افزایشی فلزات بر پایه لیزر به این دلیل رایج شده است که قابلیت تولید قطعه با کیفیت بالا و در عین حال هزینه نسبتا پایین را دارد. اما سایر منابع انرژی برای ذوب آنی پودر و یا سیم با مشکلاتی مواجه هستند، مثلا در روش باریکه الکترونی لازم است تا میزان خلا زیادی ایجاد شود تا فرآیند ساخت افزایشی انجام شود.
ساخت افزایشی با منبع انرژی اشعه لیزر
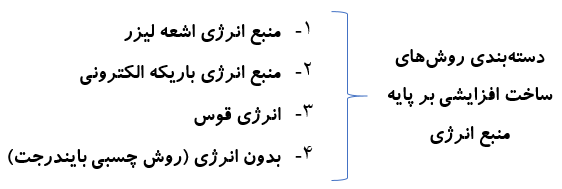
پس ساخت افزایشی فلزات با استفاده از منبع انرژی لیزر یکی از رایجترین روشهای صنعتی در این زمینه است. ساخت افزایشی فلزات مبتنی بر لیزر، به عنوان رایجترین روش صنعتی میتواند به دو صورت 1) بستر پودر 2) رسوب انرژی مستقیم صورت میگیرد.
روش بستر پودر
همانطور که از نام فرآیند پیداست ماده اولیه مصرفی در این روش، پودر فلز میباشد. در این روش یک لایه نازک از پودر فلزی بر روی یک میز پخش میشود. سپس اشعه به نقاط مشخصی از لایه پودری میتابد. تابش اشعه لیزر به هر نقطه باعث ذوب شدن پودرهای همان قسمت میشود. با دور شدن اشعه لیزر بلافاصله نقطه ذوب شده منجمد میشود. این ذوب نقطهای و انجماد پس از آن موجب میشود نقاطی که تحت تابش اشعه لیزر قرار گرفته به هم جوش بخورند و به صورت یکپارچهای به هم متصل شوند. به این صورت یک لایه ابتدایی از هندسه شکل ساخته میشود. سپس یک لایه دیگر از پودر بر روی لایه قبلی پخش میشود، دوباره با تابش اشعه لیزر پودرهای محلی که تحت تابش قرار گرفته به یکدیگر و به لایه زیرین خود جوش خورده و متصل میشوند. این فرآیند پخش پودر، تابش اشعه لیزر و ساخت یک لایه جدید، آنقدر تکرار میشود تا کل لایههای قطعه بر روی یکدیگر ساخته شود. با ساخت آخرین لایه، قطعه نهایی تشکیل میشود. همانطور که انتظار میرود در اطراف قطعه پر از پودرهای اضافی قرار دارد. در زیر فیلمی از روش ساخت افزایشی در بستر پودر را با هم میبینیم.
در مکانیزم دستگاه ساخت افزایشی بستر پودر میبینیم که یک محفظه پودر اولیه به عنوان تغذیه پودر فلزی فرآیند ساخت است و یک میز ساخت نیز قرار درد که باید پودر فلزی بر روی آن پخش شود. پس از تابش اشعه لیزر و بنابراین شکلگیری هر لایه از قطعه، برای ساخت لایه بعدی محفظه پودر اولیه کمی به سمت بالا و میز ساخت کمی به سمت پایین حرکت میکند. شکل زیر را ببینید.
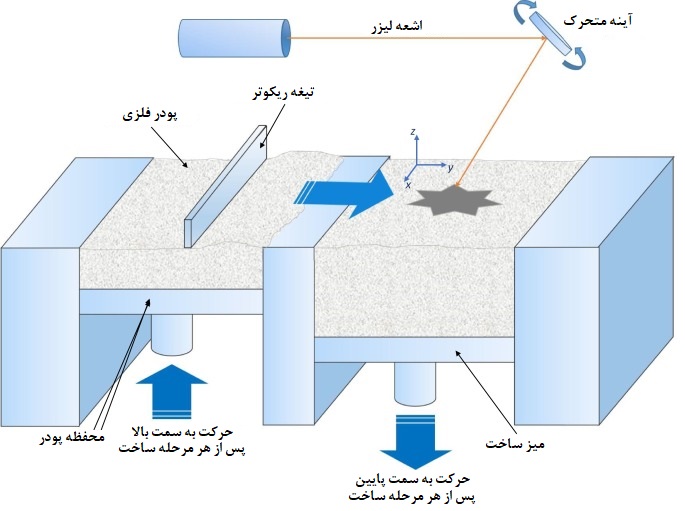
نحوه کار دستگاه به این صورت است که محفظه پودر کمی به سمت بالا حرکت میکند تا پودر کمی از لبه میز بالاتر بیاید سپس پودر توسط ریکوتر روی میز پخش میشود. پس از تابش اشعه لیزر و ساخته شدن لایه اول، میز ساخت کمی به سمت پایین حرکت میکند تا دوباره فرآیند پخش پودر صورت گیرد و لایه بعدی بر روی آن ساخته شود.
برای اطلاعات بیشتر در این زمینه زمینه میتوانید به صفحه روش بستر پودر رجوع کنید.
روش رسوب انرژی مستقیم Direct Energy Deposition (DED)
در این روش یک مجرا برای اسپری پودر فلزی در کنار اشعه لیزر وجود دارد. در واقع پودر فلزی به سطح قطعهای که در حال ساخت آن هستیم اسپری می شود و همزمان اشعه لیزر نیز پودر اسپری شده را ذوب میکند. تصویر زیر را ببینید.
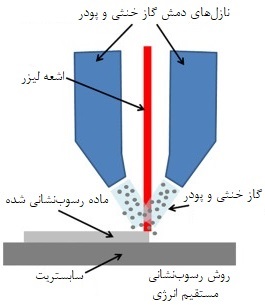
برای جلوگیری از اکسیداسیون پودر ذوب شده، از دمش گاز آرگون استفاده میشود. گاز آرگون علاوه بر جلوگیری از اکسیداسیون وظیفه اسپری پودر را نیز بر عهده دارد. در واقع حرکت پودر توسط فشار گاز آرگون انجام میشود. به همین دلیل به این روش، ساخت افزایشی بستر سیال نیز گفته میشود.
تنها مقدار کمی از پودر اسپری شده توسط اشعه لیزر ذوب میشود. پودر اضافی دمیده شده از اکسیداسیون پودرهای ذوب شده جلوگیری میکند. پودر اضافی دمیده شده از نازل قابل بازیافت است و عمده این پودر مجددا استفاده میشود.
در این روش عمدتا سایز پودر مورد استفاده نسبت به روش بستر پودر درشتتر است. در روش بستر سیال سایز پودر عمدتا در حدود 200 میکرون است در حالی که در روش بستر پودر سایز پودر عمدتا زیر 80 میکرون است. با توجه به سایز درشت پودر در روش بستر پودر، زبری سطح قطعه نهایی زیاد است. عمدتا قطعات تولید شده نهایی در ساخت افزایشی پودری زبری سطح بالایی دارند و پس از تولید قطعه نهایی عمدتا یک ماشیکناری سطحی روی قطعات برای صاف کردن سطح انجام میشود.
دستگاه ساخت افزایشی رسوب انرژی مستقیم به آسانی قابل تولید است و الزامی به خریداری این دستگاه نیست. میتوان با استفاده از یک دستگاه CNC شش محوره، مدل های پیشرفته سیستم رسوب انرژی مستقیم را تولید نمود. برای تولید این سیستم، باید کپسول دمش گاز خنثی، محفظه دمش پودر و یک لیزر بر ماشین CNC نصب نمود. قطعات ساخته شده با روش بستر سیال محدودیت ابعادی ندارند و گاها از بازوهای روباتیک برای حرکت نازل دمش پودر و اشعه لیزر استفاده میشود. شکل زیر یک نمونه دستگاه رسوب انرژی مستقیم است که در حال تولید یک مخزن با ابعاد بزرگ است. در واقع بر خلاف روش SLM که ابعاد قطعه ساخته شده به ابعاد میز ساخت محدود است، در روش بستر سیال (DED) محدودیت خاصی برای ابعاد قطعه تولیدی وجود ندارد.
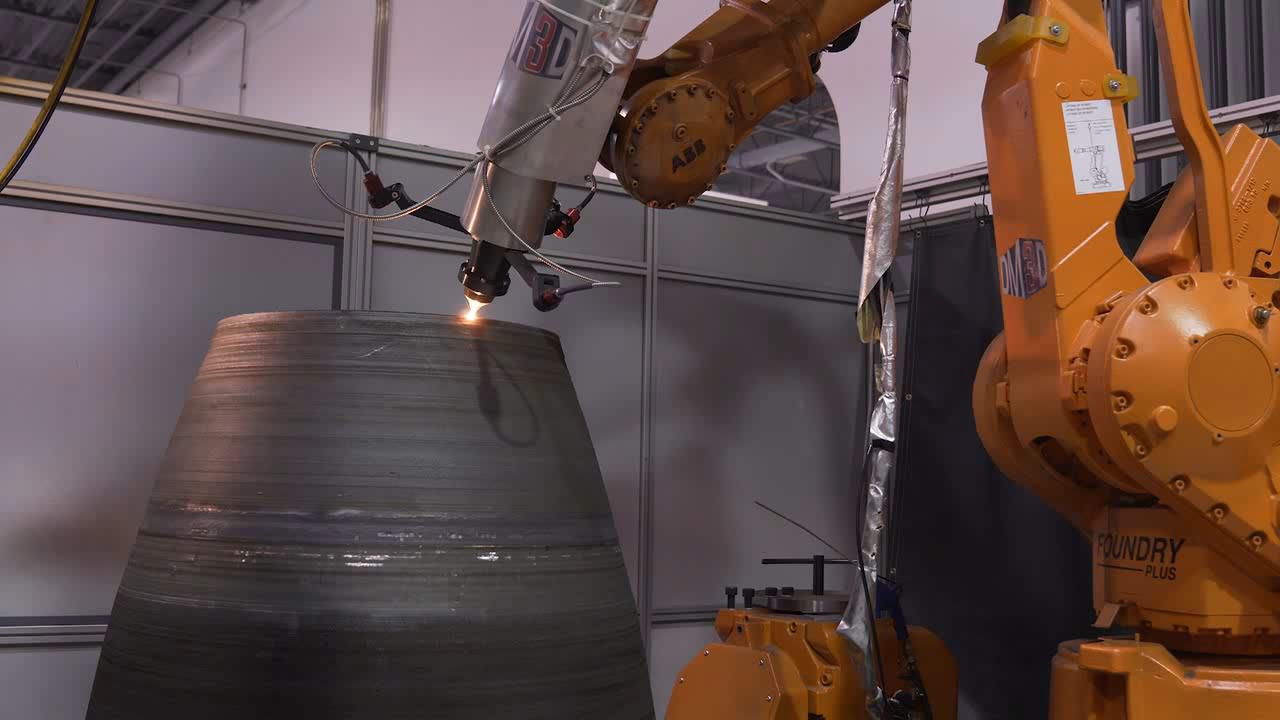
این روش با نام های Direct Laser Deposition (DLD) و Direct Metal Deposition (DMD) نیز شناخته میشود. این روش نامهای بسیار زیادی دارد و در واقع هر تولید کننده نام اختصاصی خود را بر روی روش گذاشته است. نامهای laser cladding، Laser Metal Forming (LMF) و همچنین نام معروف LENS مخفف Laser Engineering Net Shaping نیز از برخی دیگر از نامهای رایج این روش هستند.
ما عمدتا در این وبسایت این روش را با عنوان DLD ذکر میکنیم.
روش DLD مزایای خاصی را در ساخت افزایشی ایجاد میکند. یکی از مهمترین مزیتهای روش DLD امکان استفاده از این روش در فرآیندهای تعمیر قطعات صنعتی است. تصور کنید قسمت هایی از یک قطعه صنعتی دچار شکستگی شده باشد و دیگر قابلیت کاری خود را از دست داده باشد. چنانچه بتوان قسمت شکسته قطعه را با استفاده از این روش بازسازی نمود میتوان تا حد زیادی در کاهش هزینههای صنعتی صرفه جویی نمود.
دستگاه DLD ممکن است به جای یک نازل، چند نازل پودر داشته باشد.
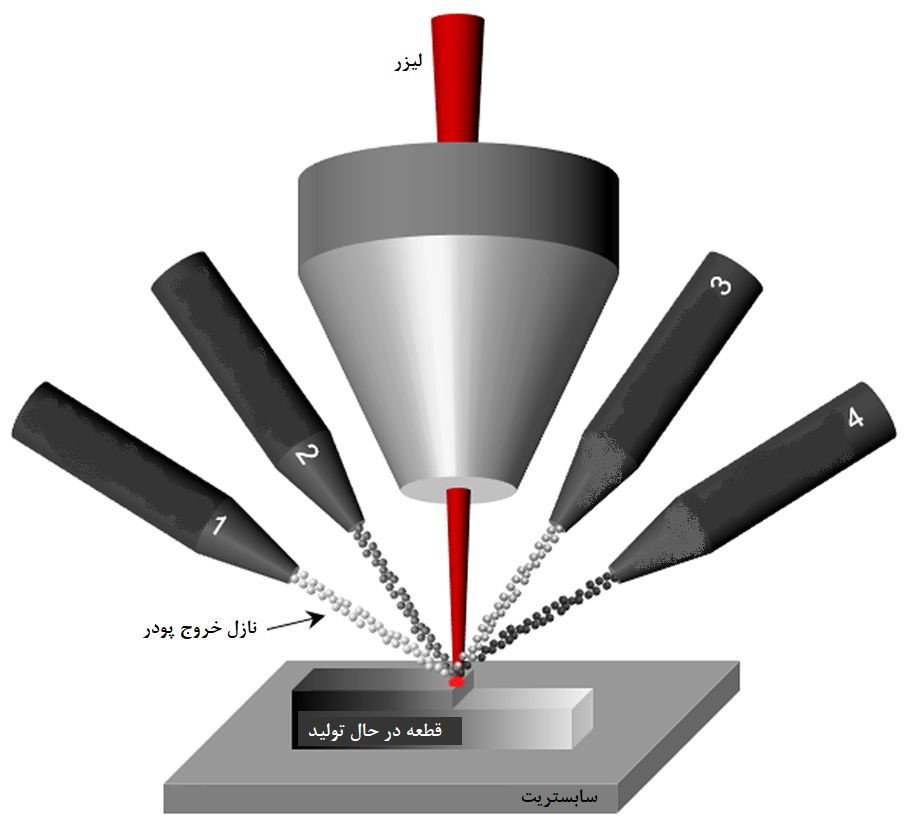
هر نازل میتواند به صورت جداگانه دمش پودر فلزی متفاوتی را داشته باشد. سرعت دمش هر پودر نیز میتواند جداگانه تنظیم شود و بنابراین میزان مصرف از هر جنس پودر قابل تعیین است. این دستگاه برای ساخت قطعات چندآلیاژی (Graded) مناسب است.
در روش بستر سیال، به جای ماده اولیه پودری، از سیم نیز میتوان برای ساخت قطعات استفاده نمود.
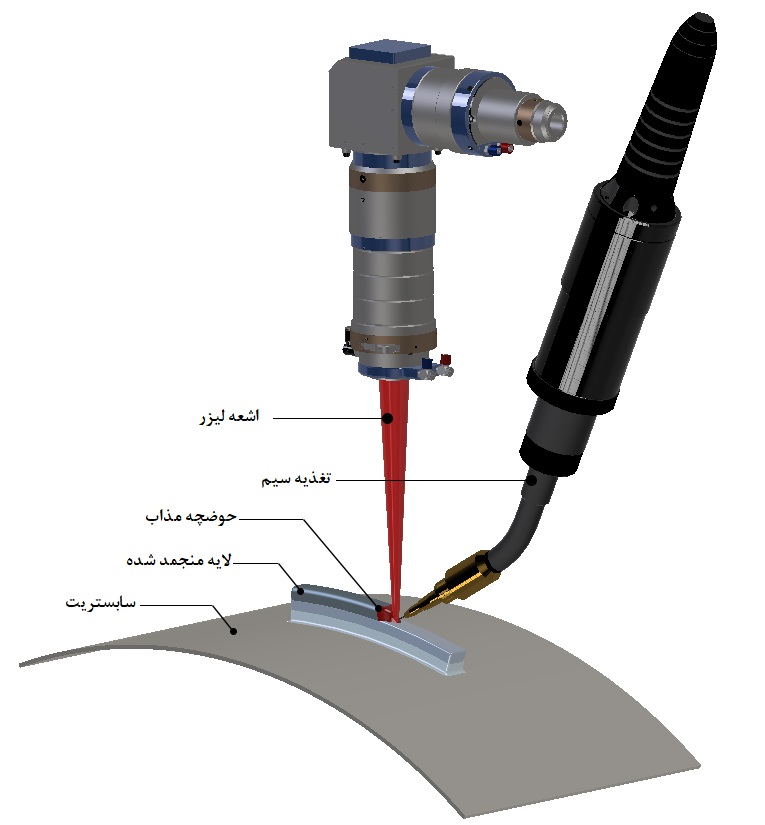
اما گفتیم که در ساخت افزایشی منبع انرژی میتواند لیزر، باریکه الکترونی، قوس و حتی بدون انرژی یعنی روش بایندرجت باشد. روش بایندر جت در مصارف عمومی کاربرد زیادی پیدا کرده است. در ادامه تصاویری از برخی برندهای معتبر این دستگاه را میبینید.
ساخت افزایشی به روش بایندرجت (binder jetting)
این روش تا حد زیادی مشابه پرینت و چاپ بر روی کاغذ است و از همین رو شرکتهای تولید پرینتر جوهرافشان همچون شرکت معروف hp در این زمینه پیشگام هستند. دستگاه ساخت افزایشی بایندر جت از پودر فلزی و چسب به عنوان ماده اولیه مصرفی تولید قطعه استفاده میکند. در این دستگاه پودرهای فلزی بر روی یک صفحه پخش میشوند. سپس توسط نازلهای سوزنی بسیار زیادی چسب بر روی پودر در قسمتهایی که باید قطعه ساخته شود پاشیده میشود. به این صورت یک لایه از قطعه ساخت می شود. سپس دوباره یک لایه پودر بر روی لایه قبلی پخش میشود و مجددا چسب پاشیده میشود تا لایه بعدی ساخته شود. این عمل آنقدر تکرار میشود تا تمامی لایههای قطعه به هم چسبیده و ساخته شوند. پس از ساخت آخرین لایه، پودرهای اضافی اطراف قطعه تمیز میشوند و قطعه درون محلول شست و شو قرار میگیرد. این محلول باعث می شود تا چسبهای اضافی اطراف قطعه تا حدی پاک شوند و کمی تخلخل درون قطعه ایجاد شود. سپس قطعه درون یک محفظه با دمای حدود 1000 درجه قرار میگیرد تا قطعه زینتر شود و چسبهای موجود در قطعه تبخیر میشود. بنابراین در این مرحله پودرهای فلزی زینتر شده و قطعه نهایی شکل میگیرد. بسته به میزان چسب مصرفی در مرحله پرینت، قطعه نهایی پس از تبخیر چسب کمی تخلخل دارد و کمی جمع میشود. قطعات نهایی شکل گرفته در این روش تا حدود 50 درصد استحکام قطعه فلزی ریخته گری شده را دارند. ممکن است بسته به برند دستگاه بایندرجت، میزان چسب مصرفی کمتر یا بیشتر شود. همچنین ممکن است برخی مراحل همچون مرحله ماده شوینده حذف شود و قطعه پس از تولید در دستگاه بایندرجت مستقیما درون کوره جهت زینترینگ قرار گیرد. با توجه به کاهش میزان چسب، میزان تخلخل و جمع شوندگی قطعه نیز کاهش مییابد و بنابراین میزان استحکام قطعه نیز تا حدی بیشتر میشود. با توجه به میزان استحکام کم قطعات تولید شده در روش بایندر جت، این روش برای تولید قطعات صنعتی که نیاز به استحکام بالایی دارند چندان مناسب نیست.